[十年]水泥及矿渣微粉高效粉磨工艺探讨
摘要:本文以大量工业生产及实验数据探讨了传统的水泥及矿渣微粉粉磨工艺与高效节能的“料床粉磨工艺”的比较,认为:目前应用广泛的挤压联合粉磨工艺将会逐步向立磨粉磨工艺过渡。
关键词:料床粉磨 立磨 辊压机 筒辊磨
导言
自1883年磨机问世以来,已被广泛用于水泥及其它行业的物料粉磨,在目前仍占有主导地位。传统的水泥及矿渣微粉制备多采用管磨机粉磨工艺,由于其粉磨空间开放、四周不限,无法形成稳定的料床,故粉磨效率低、单位粉磨电耗高、粉磨成本高。
随着科学技术的快速进步,以粉磨时间短、粒度均匀的“料床粉磨”技术为代表的高效低能耗粉磨工艺及设备已成为当今水泥工业粉磨技术发展的主流。辊压机、立磨、筒辊磨等高效率料床粉磨设备,正在逐步取代传统的管磨机,用于水泥生产线中的生料、煤粉制备及水泥、矿渣微粉的终粉磨,并获得了良好的技术经济效果。
本文探讨了水泥及矿渣微粉传统粉磨工艺与料床粉磨工艺的比较,文中不妥之处,恳望各位同仁予以批评指正。
不同粉磨工艺及其特点比较
如前所述,以管磨机为代表的传统粉磨工艺,已有一百多年历史,粉磨过程将电能转化为机械能的同时,产生的声和热,消耗了大量电能,导致单位产品电耗居高不下,尤其是当入磨物料粒度大、易磨性差或水份大时,磨机粉磨效率显著降低,更加剧了这一恶性循环。所以,管磨机在水泥工业中的应用已受到高效能料床粉磨设备的挑战,并将会逐步退出粉磨领域。
表1 管磨机与立磨、辊压机、筒辊磨粉磨特性对比
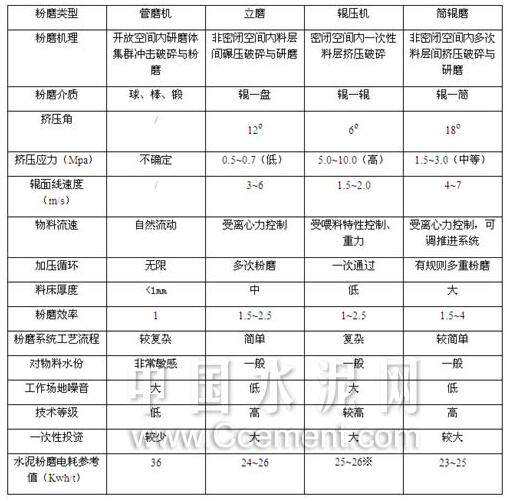
※指联合粉磨系统电耗;辊压机终粉磨电耗在21~22Kwh/t;
从表1中数据分析认为:采用料床粉磨设备终粉磨水泥(或矿渣)时,其电耗基本相当,但比管磨机系统节电约30%以上,除辊压机工艺系统较为复杂外,立磨与筒辊磨工艺系统比管磨机系统更简单些。
从目前国内新建的新型干法水泥生产线来看,大多数生料制备系统采用立磨工艺,单位粉磨电耗<15kwh/t;同时,立磨自身集烘干、破碎、粉磨、选粉、收集、输送功能于一体、占地面积小、粉磨效率高、电耗低且运行稳定而成为首选机型。辊压机用于生料终粉磨,单位电耗低于立磨,因系统复杂程度及技术含量高,维护管理工作量大,国内采用的厂家极少。筒辊磨多用于水泥粉磨系统,但国内应用厂家也很少。
采用料床粉磨工艺终粉磨产品性能
就当前而言,立磨、辊压机、筒辊磨三种料床粉磨设备都可以用于水泥及矿渣微粉的终粉磨。现以立磨为例,世界各知名公司的立磨都有其自主知识产权,磨机内部结构不尽相同、各有千秋。国外立磨结构形式见表2:
表2 国外立磨基本结构形式
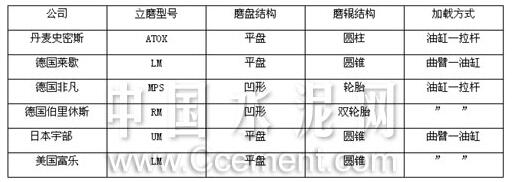
国内天津院、合肥院及中信重机、沈重等科研院所及大形设备制造厂家都推出了各自研发的立磨并应用于新型干法水泥生产线,近悉:天津院的TRM5341立磨成功用于辽宁富山5000t/d线生料系统、合肥院的HRM4800立磨成功用于浙江虎山集团5000t/d线生料制备,前几年沈重生产的MLS4531立磨用于铜陵海螺5000t/d线磨制生料、中信重机也推出了LGMS4624立磨(磨制矿渣粉为90t/h、粉磨水泥熟料为120t/h)等,标志着我国大型水泥粉磨设备的研发、制造能力已同步于世界先进水平。
料床粉磨技术发展过程中,尤其在水泥终粉磨初期,曾经遇到磨细后的水泥成品,颗粒级配范围窄、均匀性系数大、标准稠度需水量大、凝结时间过快等,立磨和辊压机的终粉磨均经历过此现象。筒辊磨问世较晚,在研发过程中鉴于前两种设备终粉磨出现的问题,在生产中加大了循环量,并通过调节其他工艺参数,较好地解决了这些问题。
墨西哥某厂采用Polysuis RMC-51/26立磨配用Sepol RMC435高效选粉机磨制纯硅酸盐水泥,系统电耗25.2Kwh/t,比闭路磨系统节电50%以上,水泥质量良好。
表3 水泥性能检测结果

FLS公司引进小野田和神户制钢联合开发并改进的OK立磨广泛用于粉磨水泥及矿渣微粉,其磨辊呈曲面,带曲面凹槽的磨盘及磨辊在粉磨过程中可及时排出料床中的压缩空气,稳定料床及减少磨振。检修时,磨辊可通过操作磨体外油缸将其翻至磨外,便于维护。
表4 台湾某厂OK19-3立磨生产的水泥性能
表中数据说明:在凝结时间、标准稠度需水量基本相同的前提下,OK磨磨制的水泥28d抗压强度比球磨水泥高出15%,同时,水泥的早期强度也高,可进一步增加混合材掺量,降低水泥生产成本。
OK磨工作时,可通过调节磨盘转速、辊压、选粉机转速、气流速度及磨内挡料圈高度等工艺技术参数达到调节水泥颗粒级配的目的,操作非常方便。采用OK磨制备比表面积400~500m
2/kg矿渣微粉时,与管磨机系统相比,OK磨粉磨电耗降低35~45%,节能潜力巨大,生产成本显著下降。
国内某公司采用进口立磨粉磨新型干法窑熟料制备不同强度等级的水泥,其实物质量数据见表5:
表5 立磨生产的水泥质量检测结果
表5数据进一步证实了国内现阶段采用立磨终粉磨,已解决了水泥标准稠度需水量过大、颗粒级配范围窄(均匀性系数n值偏大)等相关技术问题。
关于矿渣微粉粉磨工艺
随着高性能混凝土技术的发展与应用,矿渣微粉已成为混凝土制备中不可或缺的第六组分材料(人工矿物掺合料)。粒化高炉矿渣系冶炼生铁时排出的工业废渣,每生产一吨生铁,大约排出300~1000kg矿渣,其矿物成份在Cao-Sio2-Al2o3三元相图中处于C2AS、CAS2、CS、C2S结晶区,大致化学成份为CaO34~46%、SiO222~40%、Al2O35~15、MgO2~13%,并含有少量FeO、MnO、S及TiO2和金属铁。矿渣出炉时经水淬急冷,保留了微晶态的高活性玻璃体结构,其有较高的潜在物理化学活性,在含有硫、碱成份的水化环境中可激发出良好的水硬活性(如前苏联研究的碱-矿渣高强水泥属此类),可将矿渣看作是一种经过高温煅烧的高硅、低钙熟料。矿渣采用机械力活化,磨细制得的微米级粉体,具有潜在水硬性矿物的晶格产生畸变,发挥出优良的水化胶凝活性。磨细矿渣微粉掺入水泥中的强度试验结果见表6:
表6 磨细矿渣微粉掺入水泥中的胶砂强度
由表6数据可以看出:在含有矿渣配比20%的425矿渣水泥中掺入磨细矿渣微粉取代等量水泥后,水泥的早、后期强度非但没有降低,反而有显著的提高,充分说明磨细矿渣微粉具有优良的潜在水硬活性,在水泥生产过程中对改善产品的物理力学性能具有重要意义。近年来,磨细矿渣微粉作为高活性矿物掺合料,已广泛应用于高性能、高强混凝土,并对其技术机理的研究逐步微观化、系统化、深入化。不同比表面积磨细矿渣微粉应用于混凝土中的试验数据见表7:
表7 不同比表面积矿渣粉砼的物理性能
由表7可知:在水泥用量基本相同的混凝土中,当矿渣微粉的掺入量也基本相同时,混凝土的强度随矿渣微粉比表面积的提高而提高。
掺有磨细矿渣微粉的水泥及混凝土具有优良的抗渗性能和抗硫酸盐侵蚀性能,后期增进率高,大幅度提高了水泥石及混凝土的致密程度,尤其适用于潮湿环境中及大体积水工混凝土的制备。国外,在海工混凝土配制过程中就大量掺用磨细矿渣微粉,可以显著提高混凝土抵抗有害化学离子侵蚀能力及混凝土的耐久性与使用寿命。当磨细矿渣微粉取代等量水泥掺入混凝土后,混凝土水化体系放热明显减少,内、外部温差进一步缩小,降低了混凝土产生开裂的机率。同时,由于整个水化体系中碱含量降低,为有效防止混凝土碱-骨料反应(AAR)的发生创造了良好的先决条件。
矿渣微观属高活性玻璃体结构,显微硬度大(HV650左右)、韧性好、易磨性差,即易碎难磨细。采用管磨机粉磨工艺制备的比表面积≥430m
2/kg矿渣微粉时,不仅单位粉磨电耗>70kWh/t,而且研磨体消耗量大,以中铬合金材质研磨体为例,吨矿渣粉的球、锻磨耗>250-300g/t,如采用φ3.2×13m开流管磨机,磨机主电机功率为1600kW,生产比表面积≥430m2/kg矿渣微粉,台时产量也只有28t/h左右,单位粉磨电耗达72kWh/t,生产成本明显高于立磨。
近年来,国内建设的大型矿渣微粉生产线,如长钢瑞昌、莱钢鲁碧、四川等均采用了莱歇立磨粉磨工艺。如前所述,立磨集烘干、破碎、粉磨、选粉、收集、输送功能于一体,占地面积少,大大简化了生产线工艺布置。据了解,这些立磨生产线的单机产量一般都在150t/h以上,矿渣微粉比表面积≥450m
2/kg,单位粉磨电耗<50 kWh/t,甚至<45kWh/t ,而且磨耗也远低于管磨机系统,节电幅度>30%。
国内由天津院研制开发的第一台矿渣磨TRM3131S,用于杭州紫恒公司制备矿渣微粉,配用高效笼式选粉机,成品细度可在400~600m
2/kg范围内灵活调节,当控制矿渣微粉比表面积450m
2/kg时,立磨台时产量达52t/h,系统电耗为37.3kWh/t,制备的矿渣微粉性能见表8:
表8 TRM3131S立磨生产的矿渣微粉性能
以上事实证明:无论水泥及矿渣微粉的制备过程,传统的粉磨工艺将逐步向料床粉磨工艺过渡,立磨、辊压机、筒辊磨等高效粉磨设备,必将在不同场合取代现行管磨机,具有广阔的增产、节电前景。
挤压联合粉磨和筒辊磨系统
在辊压及问世之初,主要用于预粉磨流程,其功效尚不能完全发挥,加之辊压机自身存在一定的技术缺陷:辊面磨损过快、液压系统泄漏、边缘效应等,经过二十余年的发展改进以及新材料、新技术的应用,辊压机的技术性能不断得到完善,现阶段辊压机辊面工作寿命可达20000h以上,其他方面的问题也迎刃而解。
辊压机作为终粉磨设备,其电耗较低,比球磨系统节电30%以上。但存在水泥颗粒级配范围过窄、均匀性系数n值偏大、水泥凝结时间过快(石膏分布不均匀缓凝效果差所致)、成品颗粒形貌为多角形结构,导致水泥标准稠度需水量过大等。采用挤压联合粉磨工艺,主要是充分发挥辊压机的预粉磨功能,必须使辊压机多做功,才能增加挤压料中细粉的含量,辊压机多做功1kwh,后续管磨机可节省2-3kwh,管磨机能够真正发挥其特有的研磨功能,在使系统获得高产低耗的同时,对入磨粗粉水泥的多角形结构颗粒进行“整形”,改善水泥的颗粒级配,降低需水性,以确保提高水泥的使用性能。
采用挤压联合粉磨工艺可在原粉磨系统基础上增产50~150%,单位粉磨电耗较普通管磨机粉磨工艺可节省30%以上。挤压联合粉磨系统的后续管磨机有开流和圈流两种形式,同一企业采用挤压联合粉磨工艺,后续均为φ3.2×13m管磨机,开流、圈流两种不同系统制备的水泥性能见表9:
表9 挤压联合粉磨系统水泥质量检测结果

从表9得知,在相同熟料配比条件下,采用挤压联合粉磨工艺后续管磨机为开流系统时,所磨制的强度等级P.O52.5水泥早、后期强度略高于圈流系统粉磨的水泥。同时,凝结时间也要短些,水泥颗粒级配范围更宽些,开流系统单位粉磨电耗为25.7Kwh/t,圈流系统单位粉磨电耗为27.4Kwh/t。此外,圈流系统工艺略复杂些,这也许是部分企业选用开流粉磨工艺的真正原因。
国内牡丹江水泥公司2003年引进法国FCB公司研制的HoRo mill3800筒辊磨用于粉磨水泥(国内第一台应用),装机功率2400kw,配用TSV4500选粉机,设计能力120t/h,辊筒工作转速36r/min,单位粉磨电耗为24.5kwh/t。筒辊磨生产的水泥与球磨磨制的水泥物理性能对比见表10:
表10 筒辊磨与球磨磨制的水泥性能对比

表中数据可以看出:相同混合材配比条件下,与球磨水泥相比,筒辊磨磨制备的水泥有更高的早、后期强度,与立磨磨制的水泥性能基本相似,说明仍能进一步提高混合材掺量,降低生产成本。筒辊磨单位粉磨电耗比立磨更低些,显示出其特有的技术优势。在水泥物理性能方面,筒辊磨生产的水泥标准稠度需水量仍略大于球磨机磨制的水泥,这可能是筒辊磨水泥颗粒形貌大部分为扁针状,水化过程比球形颗粒更快的缘故。
结束语
5.1传统的管磨机粉磨工艺,其粉磨空间四周不限,难以形成料床,故效率低、单位粉磨电耗高、研磨体消耗大、生产成本高。目前应用广泛的挤压联合粉磨系统部分引入了料床粉磨工艺,属成熟的节能工艺技术,但工艺系统布局较为复杂,随着时间的推移,将会逐步向立磨终粉磨过渡。
5.2立磨、辊压机、筒辊磨均为料床粉磨的高效节电设备,实现了无球化终粉磨,用于制备水泥和矿渣微粉,相对传统管磨机粉磨工艺而言,节电幅度达30~40%以上,更有利于节能减排,发展循环经济,功在当代,利在千秋。
5.3立磨集烘干、破碎、粉磨、选粉、收集、输送于一体,并已率先实现大型化,工艺流程简单、占地面积小,单位粉磨电耗和金属磨耗低,是当前大、中型水泥及矿渣微粉制备企业首选的高效粉磨工艺设备。
5.4立磨、筒辊磨与传统管磨机粉磨工艺所制备的水泥力学性能相比,具有更高的早、后期强度,可以增加混合材掺加量、降低吨位水泥制造成本,综合提高经济效益。同时,由于大量掺用工业废渣,有利于净化环境、消除废渣污染。
5.5无论磨制水泥或矿渣微粉,要求磨前设置多道强力除铁,由于单质铁粒具有铁磁性和可塑性,难以磨细的同时在磨内产生富集,加剧设备磨损,必须予以除去。以使粉磨系统保持较高而稳定的粉磨效率,有效降低主机设备磨损,延长工作寿命。
说明:本文撰写过程中,参考并引用了水泥界老师们著作中的部分数据,在此向各位老师致以深深的谢意!
参考文献
【1】.张路明,《国内立磨发展概况及LGMS4626矿渣立磨的研制与使用》,《矿山机械》2008.3【2】.赵乃仁,《Polysuis立磨粉磨水泥》,《水泥工程》2004.3
【3】.熊会思、熊然《新型干法水泥厂设备选型使用手册》,中国建材工业出版社2007年1月第一版
【4】. 柴星腾,《TRM矿渣辊磨的研制与应用》,《中国建材报·机械与装备》2008.5.20头版
【5】. 任林燕,《Horomill与球磨机磨制的水泥性能对比》,《水泥》2004.6
摘自:中国建材工业经济研究会水泥专业委员会 邹伟斌